5. Carbon Dioxide Emissions and Land Useage from Ethanol Production 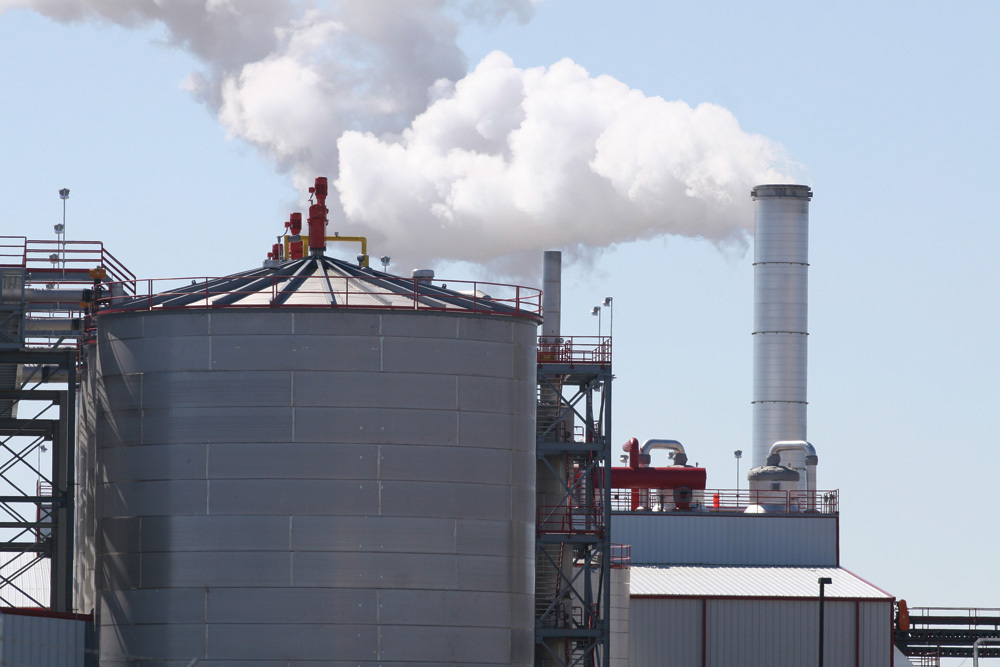
To produce ethanol in the US, corn is fermented, whereas in Brazil sugarcane is fermented. The fermentation process is highly CO2 intensive, i.e., it creates a lot of carbon dioxide.
5.1. Not all ethanol plants are the same
In 2007 Brazilian and U.S. mills produced 5.3 and 6.5 billion gal, respectively. We compare below the CO2 emissions savings attained from plants in the US and Brazil. As of 2010, it is clear that the life cycle GHG emissions savings in Brazil is twice that in the US.
Helena Chum US and Brazil Bilateral Collaboration on Biofuels NREL Dec 12, 2012.
The plot below again compares North American Corn Ethanol with Brazilian Sugarcane Ethanol. From a percentage of GHG reduction point of view, the details of the process used makes a lot of difference. Clearly using coal produces the most greenhouse gases. Natural gas can reduce GHG by 40%. We see that from a GHG perspective we can only get into the same ballpark as Brazil of 75-100% GHG reduction by moving to advanced processes, that can ferment cellulosic feedstocks like corn stover.
On the net energy ratio axis, it is clear the current natural gas based distilleries produce more energy than is in the input feedstock (reference the dotted blue line at the break even point). But to get the Net Energy Ratio of 10 and their projected NER of 12 is not possible in the contiguous 48 states with ethanol based around corn.
So how much carbon dioxide is currently emitted? As of Sept 2012, large corn ethanol plants are considered “major emitters” under EPA rules because one-third of the corn kernel, by weight, is released as carbon dioxide during fermentation. About 19 pounds of it per bushel.
However, Hawaii, with a climate that loves sugarcane, could be a different story if modern (Brazilian inspired) techniques are introduced, as we see in the chart below.
Below we examine land energy productivity/ha harvested. The GHG savings and land energy productivity of both the US and brazilian ethanol systems have improved significantly due to continued adoption of more efficient technologies over time. To read the chart, note that the blue bars go with the blue scale of GHG Emissions at the top, and the red bars go with the land productivity scale at the bottom. As land energy productivity increases, the GHG emissions savings increases.
Advanced future systems are expected to continue to improve their environmental performance. However, how far these improvements reach depends on factors such as the assumed technologies, agricultural practices, technological learning, and how the crops and associated residues will be used to produce different combinations of products. As such, biofuel water and land use footprints can only be understood within these contexts. We will discuss this more below. Once again, it is interesting that the land use productivity growing sugar cane in Brazil is significantly higher.
5.2. US plants
5.2.1. Current State
The US usage of ethanol has steadily increased. The plot below, however, shows that its growth is slowing down. It is at approximately 10% of our fuel usage,and distributed into most gasoline as E10.
Although corn ethanol has progressed a great deal in efficiency over the last 10 years the carbon dioxide emissions remain. In fact, large corn ethanol plants are considered “major emitters” under EPA rules because one-third of the corn kernel, by weight, is released as carbon dioxide during fermentation. About 19 pounds of it per bushel. This is illustrated above. Finding a use for this CO2 is a major area of research and development. As the chart shows one possibility is to help grow algae.
5.2.2. Future of Ethanol in the US
5.2.2.1. Farm units integration
Integrating corn ethanol with dairy, poultry and livestock feeding operations is an opportunity to mitigate the methane coming off the manure, and to convert that into biogas. This displaces natural gas for production power. Integrated “wet distillers grains”, fed to adjacent livestock, requires no expensive drying, and this substantially reduces energy consumption and increases its nutritional quality over dried distillers grains. This is a high protein feed supplement that makes-up 20-30% of the diet, which enhances milk, poultry, fish and meat production. To make ethanol, we basically remove the starch, the component that most livestock do not fully digest. Now we will remove most of the oil as well, and this will make the proteins even more digestible and efficient.
5.2.2.2. Production of Yeast
5.2.2.3. Combining fermentation with growing and using algae.
A combination that is not obvious, but may be very important in ethanol production is to use the waste CO2, waste heat, and waste effluent to grow algae. We will also see algae being integrated with corn ethanol, an ideal combination. Both Nebraska and Iowa have funded research projects to integrate algae into corn ethanol. Green Plains, one of the most successful corn ethanol producers, already has an algae unit on the ground adjacent to a corn ethanol refinery – producing additional onsite feedstock from waste products. This is the future of corn ethanol.
The companies BioProcess Algae and Green Plains Renewable Energy are aiming for a “lowest-cost winner” in algae biofuels. They are growing algae in modified greenhouses. It’s hybrid design – a semi-closed system, using some elements of greenhouse design to protect and warm the algae, but using the some of the best, low-cost aspects of raceway-style, open pond design. That gives it a cost structure and a system that works in the temperate climates where staple grains generally grow — makes it possible to put the plant next to the CO2 source and share infrastructure. The 5-acre demonstration is shown below right, below left is the view inside one of them. The sketch shows how the algae growing on the rough surfaces is turned into the liquid, and exposed to the sun. CO2 is pipe into the center of the rollers.
They are already ready to move to larger scale. So what are the next steps? Following completion of the 5-acre demonstration, the company will proceed to full-commercial scale. And that can be substantial. A 100 million gallon corn ethanol plant produces enough CO2 to support 140,000 tons of algae production. Even at 60 tons per acre per year (as Cellana has generated at its 6-acre facility), that’s up to 2300 acres of algae production from a single site – almost 4 square miles. Possible? Depends entirely on site characteristics. But you get the idea.
5.2.4. Actively using the CO2, and a hint at the future.
Irrespective of technology, these are projects that monetize CO2. That’s their fundamental magic, liberating value from a waste stream. It’s an elegant expression of a foundational value proposition of advanced biofuels: “Less is more. Use what is there to the extent possible.” The value proposition, in terms of capturing and liberating value, is substantial. Let’s look at the hard data. In the United States, there is 14 billion gallons of corn ethanol capacity, which in turn represents the processing of around 4.8 billion bushels of corn (at 2.9 bushels per gallon), and generates 43.2 million tons of CO2 (at 18 pounds per bushel). How much value?
Australia has priced carbon at $A 23 per tonne; US advanced biotechnology developers like Algenol have modeled their CO2 acquisition at $30 per ton. Let’s use $25 as a mid-point. That’s $1.08 billion in value, and enough CO2 to produce 21 million tons of algae. Now, it is highly tempting to do math and figure that, at a 30 percent lipid content, you could get around 1.6 billion gallons of renewable diesel by souring some added hydrogen, or the same volume of biodiesel. Or an awful lot of Omega-3s, and high value protein for animal feed. And the financial math in converting a $25 ton of CO2 into a $1000 ton of high-value feed is pretty compelling. But not every process requires harvesting and extracting value from algae. The Shenandoah Project certainly does – but we may see more projects in the future like Joule Unlimited or Algenol that feature no-kill biofuels production – where the microorganisms are milked rather than harvested – and the yields may well go 50-150 percent higher, in terms of yields per pound of CO2. But that's down road.
5.3. Brazilian plants
Forty one percent of the motor fuel in Brazil in 2011 was ethanol.
.